
To solve this, the area between the bearing and the bearing isolator must include an unobstructed return pathway to the sump. When this occurs, lubricant will accumulate in this area until the space becomes completely flooded and the seal leaks. The area between the bearing and the bearing housing seal may lack a drain channel. But the return path to the sump may be blocked by counter-bores in the housing, which were originally designed to provide a positive stop for pressed-in lip seals. Once they have collected the lubricant, they need a clear, unobstructed path to return collected lubricant back to sump. Most modern bearing isolators are effective at collecting splash lubricant in their respective labyrinth patterns. One of the most common causes of improper seal orientation is a lack of training or unclear installation instructions. This allows oil to easily return to the sump. This return needs to be installed at the bottom dead-center or six o’clock position of the bearing isolator for proper function. Most bearing isolators have a lubricant return designed into their respective labyrinth patterns. There may be some oil leakage as the seal clears itself of excess lubricant, but that should diminish over time. Fortunately, once returned to the proper level, bearing isolators will generally stop leaking and return to normal function. This practice can inadvertantly contribute to leakage. The thinking is that if leakage occurs, there will be extra lubricant available. It has become common practice for maintenance professionals to fill up to, if not a bit over, the maximum fill line. It seems simple, but the greatest cause of bearing isolator leakage on process pumps is an over-filled bearing housing. A bearing isolator installed on a process pump (Courtesy of Inpro/Seal) 1. Though true for contact seals, the presence of leaking oil from a bearing isolator is most likely due to factors other than seal failure.įollowing are some of the more common causes of bearing isolator lubricant leakage in process pumps.
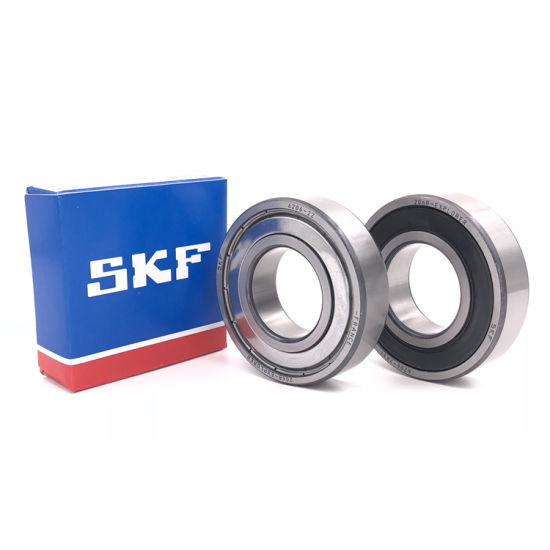
For most operators, the analysis is simple: no leaking oil means the seal is fine while leaking oil equates to failure. The most common perception of bearing housing seal failure on process pumps is lubricating oil leaking from the bearing housing. This increases mean time between repair (MTBR). Though more expensive, bearing isolators effectively retain lubricants and exclude contaminants while providing a virtually infinite life expectancy.
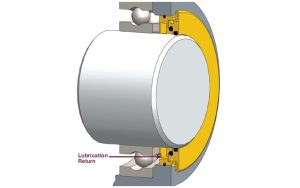
When this occurs, lubricant will escape to atmosphere and contaminants will enter the bearing housing, leading to bearing failure. Because contact seals use contact as their sealing method, they have a more limited life expectancy, since they can wear at the point of contact or groove the shaft. A well-known technique for increasing pump reliability is sealing the bearing housing with non-contacting bearing isolators rather than contact seals.
